軸承鋼盤條冷鐓套圈開裂原因分析及改進措施
2021-02-24肖訓(xùn)軍
(南京鋼鐵有限公司)
(南京鋼鐵有限公司)
前言
某用戶使用南鋼18mm規(guī)格某批次軸承鋼盤條GCr15-Y,中間經(jīng)輥底式連續(xù)爐退火,連續(xù)退火爐為氮氣保護真空鎖氣輥底式球化退火爐。
球化退火工藝流程為:來料檢驗→裝框上進料臺→進前真空室(抽空氣充氮氣)→由真空室進入預(yù)熱區(qū)、升溫區(qū)、保溫區(qū)、快冷區(qū)、等溫區(qū)、緩冷區(qū)、自由冷區(qū)(熱裝爐升溫到795℃,保溫7h,快速冷卻到720℃,保溫5h,以20℃/h冷卻速度降至650℃出爐)→進入冷水倉→進后真空室→出料臺。
退火料經(jīng)過原料檢驗→酸洗→磷皂化→輕拉一道30絲→下料冷鐓成毛坯套圈,肉眼可見套圈端面存在開裂現(xiàn)象,開裂比例在10%~15%之間,開裂位置不連續(xù),裂縫位置沿盤條徑向垂直于軋制延伸方向,如圖1所示。
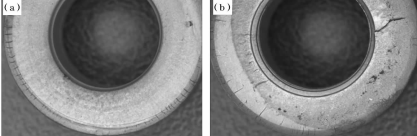
圖一
用戶反饋球化退火、拉絲、冷鐓工藝正常,只有本批次軸承鋼盤條冷鐓套圈開裂比例超出10%,與原始盤條關(guān)系較大。
盤條生產(chǎn)工藝為:坯料拋丸、點磨處理→步進式加熱爐加熱(預(yù)熱段700~750℃、加熱一段930~960℃、加熱二段1130~1160℃、均熱段1200~1240℃,加熱二段和均熱段高溫段時間60~100min。)→高壓水除鱗→粗軋→中軋→預(yù)精軋→一區(qū)水冷→精軋→二區(qū)水冷→減定徑→三區(qū)水冷→吐絲→斯泰爾摩風(fēng)冷→集卷→精整→打捆→稱重→入庫。
1 開裂套圈樣品分析
從開裂套圈樣品中隨機取4個樣,其中2個套圈用作高、低倍檢驗和硬度分析,另外2個套圈用作碳化物不均勻性及斷口檢驗、晶粒度分析。
1.1宏觀檢查
從套圈開裂樣品中隨機挑選1個,在體視顯微鏡下觀察,套圈開裂宏觀形貌如圖2所示。
1 開裂套圈樣品分析
從開裂套圈樣品中隨機取4個樣,其中2個套圈用作高、低倍檢驗和硬度分析,另外2個套圈用作碳化物不均勻性及斷口檢驗、晶粒度分析。
1.1宏觀檢查
從套圈開裂樣品中隨機挑選1個,在體視顯微鏡下觀察,套圈開裂宏觀形貌如圖2所示。
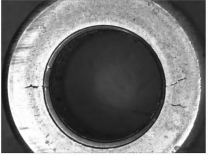
圖二
1.2低倍檢驗
將其中一個套圈在熱鹽酸(濃度31%,溫度70~80℃)中浸蝕8~10min后取出,宏觀檢查,發(fā)現(xiàn)套圈的正反兩端面均存在多條裂紋正面如圖3a所示,反面如圖3b所示。
將其中一個套圈在熱鹽酸(濃度31%,溫度70~80℃)中浸蝕8~10min后取出,宏觀檢查,發(fā)現(xiàn)套圈的正反兩端面均存在多條裂紋正面如圖3a所示,反面如圖3b所示。
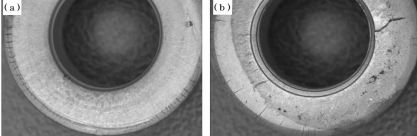
圖三
將另一個套圈試樣的一端面磨去2~3mm,并沿縱截面切除一部分,在熱鹽酸(濃度31%,溫度70~80℃)中浸蝕8~10分鐘后取出,按國標(biāo)/GBT18254評定中心疏松和一般疏松均為1.0級,未見縮孔缺陷存在,形貌如圖4所示。因此套圈端面開裂與原材料低倍組織無關(guān)。

圖四
1.3高倍檢驗
1.3.1套圈裂紋退火態(tài)檢驗
在圖2右側(cè)端面兩條裂紋處取樣經(jīng)打磨制備后,顯微鏡下觀察縱截面,開裂的裂紋內(nèi)及周圍均未見夾雜物、氧化物存在,腐蝕后觀察,裂紋兩側(cè)與基體顯微組織一致,為鐵素體基體上分布著球粒狀珠光體,試樣邊緣與裂紋處均未見脫碳現(xiàn)象,如圖5所示裂紋對面端面取樣制備后觀察,橫截面上的裂紋兩側(cè)與基體顯微組織一致,為鐵素體基體上分布著球粒狀珠光體,如圖5所示。
1.3.1套圈裂紋退火態(tài)檢驗
在圖2右側(cè)端面兩條裂紋處取樣經(jīng)打磨制備后,顯微鏡下觀察縱截面,開裂的裂紋內(nèi)及周圍均未見夾雜物、氧化物存在,腐蝕后觀察,裂紋兩側(cè)與基體顯微組織一致,為鐵素體基體上分布著球粒狀珠光體,試樣邊緣與裂紋處均未見脫碳現(xiàn)象,如圖5所示裂紋對面端面取樣制備后觀察,橫截面上的裂紋兩側(cè)與基體顯微組織一致,為鐵素體基體上分布著球粒狀珠光體,如圖5所示。
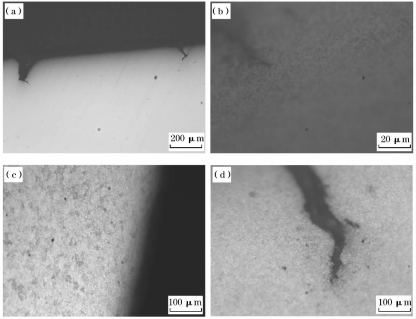
圖五
1.3.2碳化物不均勻檢驗
將一套圈經(jīng)淬回火處理后,在顯微鏡下檢驗縱截面碳化物不均勻性,發(fā)現(xiàn)帶狀、網(wǎng)狀形貌如圖6所示,按國標(biāo)GB/T18254評定為帶狀級,網(wǎng)狀1.5級,未見碳化物液析存在,滿足國標(biāo)要求。因此套圈端面開裂與原材料碳化物均勻性無關(guān)。
將一套圈經(jīng)淬回火處理后,在顯微鏡下檢驗縱截面碳化物不均勻性,發(fā)現(xiàn)帶狀、網(wǎng)狀形貌如圖6所示,按國標(biāo)GB/T18254評定為帶狀級,網(wǎng)狀1.5級,未見碳化物液析存在,滿足國標(biāo)要求。因此套圈端面開裂與原材料碳化物均勻性無關(guān)。
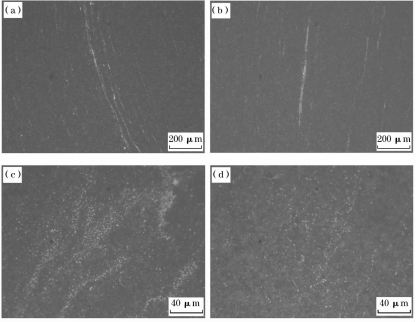
圖六
1.4套圈布氏硬度檢驗
沿套圈圓環(huán)方向隨機進行布氏硬度檢測,硬度較為均勻,平均硬度為290.8HB,未發(fā)現(xiàn)明顯的高點或低點,檢測數(shù)據(jù)如表1所示。
沿套圈圓環(huán)方向隨機進行布氏硬度檢測,硬度較為均勻,平均硬度為290.8HB,未發(fā)現(xiàn)明顯的高點或低點,檢測數(shù)據(jù)如表1所示。

1.5套圈斷口檢驗
一套圈經(jīng)淬火處理后,一次擊斷,借助體視顯微鏡檢驗套圈縱截面斷口組織,在宏觀斷口表面上有許多亮面,每個亮面都是一個晶粒的界面,斷裂路徑沿著不同位向的晶界延伸,為典型的沿晶脆性斷裂,形貌如圖7所示。
根據(jù)斷裂能量消耗最小原理,裂紋的擴展路徑總是沿著原子鍵合力最薄弱的表面延伸,在很大程度上取決于晶界面的狀態(tài)和性質(zhì)。晶界強度不一定最低,但如果金屬存在著某些冶金因素使晶界弱化(例如鋼坯出現(xiàn)過熱或過燒),則金屬將會發(fā)生沿晶脆性斷裂。
一套圈經(jīng)淬火處理后,一次擊斷,借助體視顯微鏡檢驗套圈縱截面斷口組織,在宏觀斷口表面上有許多亮面,每個亮面都是一個晶粒的界面,斷裂路徑沿著不同位向的晶界延伸,為典型的沿晶脆性斷裂,形貌如圖7所示。
根據(jù)斷裂能量消耗最小原理,裂紋的擴展路徑總是沿著原子鍵合力最薄弱的表面延伸,在很大程度上取決于晶界面的狀態(tài)和性質(zhì)。晶界強度不一定最低,但如果金屬存在著某些冶金因素使晶界弱化(例如鋼坯出現(xiàn)過熱或過燒),則金屬將會發(fā)生沿晶脆性斷裂。
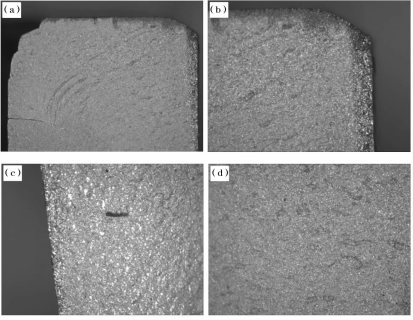
圖7
1.6套圈奧氏體晶粒度檢驗
制備斷口縱截面試樣在顯微鏡下檢驗晶粒度,發(fā)現(xiàn)套圈外壁晶粒度明顯比基體晶粒度要粗,形貌如圖8所示。因此推測斷口試樣與原始盤條加熱工藝即鋼坯在加熱過程中局部過熱有關(guān)。
制備斷口縱截面試樣在顯微鏡下檢驗晶粒度,發(fā)現(xiàn)套圈外壁晶粒度明顯比基體晶粒度要粗,形貌如圖8所示。因此推測斷口試樣與原始盤條加熱工藝即鋼坯在加熱過程中局部過熱有關(guān)。

圖八
2 缺陷盤條工藝追溯及套圈用軸承鋼盤條生產(chǎn)工藝改進
通過對開裂樣品進行低倍、硬度、碳化物、斷口、晶粒度等進行檢測,低倍組織、碳化物均勻性、表面硬度均正常,而斷口存在過熱組織,且套圈外壁晶粒度明顯比基體晶粒度要粗,推測這與原始盤條加熱工藝即鋼坯在加熱過程中局部過熱有關(guān)。
對開裂批次盤條加熱工藝進行追溯,軋制批號C60199901共47支坯料,在換軋該規(guī)格時已入爐,離爐頭僅10個步距,預(yù)熱段701~715℃,加熱一段952~959℃,加熱二段1148~1156℃,滿足工藝要求,而均熱段1245~1248℃,加熱二段和均熱段高溫段時間126分鐘,超出工藝規(guī)范上限。
為迅速解決軸承鋼盤條冷鐓套圈開裂現(xiàn)象,對軸承鋼盤條加熱工藝進行優(yōu)化:
(1)對軸承鋼坯料入爐位置進行優(yōu)化。在換輥時用于做套圈的軸承鋼坯料不允許直接進入加熱一段,第1支坯料離爐頭出鋼位置至少48個步距,如圖9所示。當(dāng)過渡鋼種不夠時,需空出足夠的步距,利用換輥時間按正常出鋼節(jié)奏走完空的步距,以防止軸承鋼坯料在爐內(nèi)加熱段長時間停留而產(chǎn)生局部過熱缺陷。
通過對開裂樣品進行低倍、硬度、碳化物、斷口、晶粒度等進行檢測,低倍組織、碳化物均勻性、表面硬度均正常,而斷口存在過熱組織,且套圈外壁晶粒度明顯比基體晶粒度要粗,推測這與原始盤條加熱工藝即鋼坯在加熱過程中局部過熱有關(guān)。
對開裂批次盤條加熱工藝進行追溯,軋制批號C60199901共47支坯料,在換軋該規(guī)格時已入爐,離爐頭僅10個步距,預(yù)熱段701~715℃,加熱一段952~959℃,加熱二段1148~1156℃,滿足工藝要求,而均熱段1245~1248℃,加熱二段和均熱段高溫段時間126分鐘,超出工藝規(guī)范上限。
為迅速解決軸承鋼盤條冷鐓套圈開裂現(xiàn)象,對軸承鋼盤條加熱工藝進行優(yōu)化:
(1)對軸承鋼坯料入爐位置進行優(yōu)化。在換輥時用于做套圈的軸承鋼坯料不允許直接進入加熱一段,第1支坯料離爐頭出鋼位置至少48個步距,如圖9所示。當(dāng)過渡鋼種不夠時,需空出足夠的步距,利用換輥時間按正常出鋼節(jié)奏走完空的步距,以防止軸承鋼坯料在爐內(nèi)加熱段長時間停留而產(chǎn)生局部過熱缺陷。
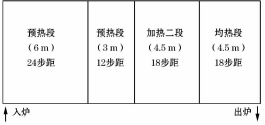
圖九
(2)對軸承鋼坯料加熱時間進行優(yōu)化,控制軸承鋼坯料在進入加熱二段和均熱段后的高溫段停留時間不超過100min。
(3)對軸承鋼坯料加熱溫度和出鋼溫度進行優(yōu)化,為避免軸承鋼坯料在爐內(nèi)高溫段出現(xiàn)局部過熱現(xiàn)象,嚴(yán)格控制加熱溫度,加熱段和均熱段的最高加熱溫度不超過1220℃,除鱗后紅鋼溫度不超過1130℃。
3 工藝改進實施效果
工藝改進后再次生產(chǎn)供某用戶生產(chǎn)18mm規(guī)格套圈用軸承鋼盤條GCr15-Y,爐號16706548共45支坯料。換軋18mm規(guī)格時該爐號坯料只入爐24支,換輥時間為50min,換輥后生產(chǎn)過程比較順利,加熱二段和均熱段的高溫段停留時間為68min,加熱二段溫度為1135℃,均熱段溫度為1212℃,除鱗后紅鋼溫度為1122℃。
取本批次盤條樣品和以往產(chǎn)生過熱缺陷的盤條做奧氏體晶粒度對比,發(fā)現(xiàn)存在過熱缺陷的盤條邊部晶粒度明顯粗大,而本次盤條晶粒度比較均勻細(xì)小,如圖10所示。
(3)對軸承鋼坯料加熱溫度和出鋼溫度進行優(yōu)化,為避免軸承鋼坯料在爐內(nèi)高溫段出現(xiàn)局部過熱現(xiàn)象,嚴(yán)格控制加熱溫度,加熱段和均熱段的最高加熱溫度不超過1220℃,除鱗后紅鋼溫度不超過1130℃。
3 工藝改進實施效果
工藝改進后再次生產(chǎn)供某用戶生產(chǎn)18mm規(guī)格套圈用軸承鋼盤條GCr15-Y,爐號16706548共45支坯料。換軋18mm規(guī)格時該爐號坯料只入爐24支,換輥時間為50min,換輥后生產(chǎn)過程比較順利,加熱二段和均熱段的高溫段停留時間為68min,加熱二段溫度為1135℃,均熱段溫度為1212℃,除鱗后紅鋼溫度為1122℃。
取本批次盤條樣品和以往產(chǎn)生過熱缺陷的盤條做奧氏體晶粒度對比,發(fā)現(xiàn)存在過熱缺陷的盤條邊部晶粒度明顯粗大,而本次盤條晶粒度比較均勻細(xì)小,如圖10所示。
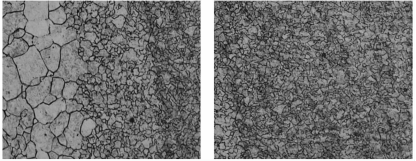
圖十
用戶使用該批盤條后未再投訴相關(guān)質(zhì)量問題,據(jù)用戶反饋冷鐓套圈過程中開裂比例明顯下降,從10%以上下降到0.5%以內(nèi)。
4 結(jié)論
軸承鋼盤條冷鐓套圈開裂與原始盤條加熱工藝即鋼坯在加熱過程中局部過熱有關(guān),在套圈用軸承鋼盤條生產(chǎn)計劃編排時應(yīng)盡量避免軸承鋼坯料在換輥時直接進入加熱一段,實在無法避免時應(yīng)按排過渡鋼種或空出相應(yīng)步距。
嚴(yán)格控制加熱溫度和加熱時間,鋼坯進入加熱二段和均熱段后的高溫段停留時間不超過100min,最高加熱溫度不超過1220℃,除鱗后紅鋼溫度不超過1130℃。
采用改進后的工藝連續(xù)生產(chǎn)多個批次,一直未出現(xiàn)批量開裂質(zhì)量投訴。
4 結(jié)論
軸承鋼盤條冷鐓套圈開裂與原始盤條加熱工藝即鋼坯在加熱過程中局部過熱有關(guān),在套圈用軸承鋼盤條生產(chǎn)計劃編排時應(yīng)盡量避免軸承鋼坯料在換輥時直接進入加熱一段,實在無法避免時應(yīng)按排過渡鋼種或空出相應(yīng)步距。
嚴(yán)格控制加熱溫度和加熱時間,鋼坯進入加熱二段和均熱段后的高溫段停留時間不超過100min,最高加熱溫度不超過1220℃,除鱗后紅鋼溫度不超過1130℃。
采用改進后的工藝連續(xù)生產(chǎn)多個批次,一直未出現(xiàn)批量開裂質(zhì)量投訴。
來源:《金屬材料與冶金工程》2016年05期